David Hobbs: British aircraft carrier design that led the world – Part 1
British aircraft carrier design that led the world
The Royal Navy designed and built the world’s first aircraft carrier, HMS Argus, in 1918. It has led the world in the design and development of the technologies that have allowed bigger and faster jets to take-off and land on their flight decks and continues to do so today.
The ‘Rubber’ Flight Deck
In 1945 deck landing trials with de Havilland Sea Vampire fighters exposed the limitations imposed by the slow acceleration rates of early types of jet engine and it became obvious that changes in both carrier technology and deck landing technique were needed. Scientists predicted that the next generation of fighters would have supersonic performance with thin, highly-swept wings designed for high performance at altitude and that such aircraft would have deck landing speeds twice that of piston-engined fighters. More flight deck space would be required for their arrested landings and, to make matters worse, the limited volume available in their thin wings would be unlikely to be able to accommodate the substantial undercarriages needed to absorb the impact velocities of deck landing at unprecedentedly high speeds. For a while in 1947 it seemed to the Admiralty that if no practical solution could be found, the operation of jet fighters from carriers would only be possible in very small numbers. Mr Lewis Boddington, Head Scientist at the Naval Aircraft Department, NAD, at the Royal Aircraft Establishment, RAE, at Farnborough recommended transferring the pneumatic absorption of deck landing stresses from the aircraft to the carrier, in other words operating aircraft that had no undercarriages. His concept was based on the logic that catapults and arrester wires, the other devices that allowed short take-offs and landings, were built into the carrier and not the aircraft. The idea had the additional merit that the airframes of fighters without undercarriages would be some 15% lighter than their conventional equivalents and this could be translated into higher performance. The obvious drawback was the inability of aircraft without wheels to move under their own power after landing either on a carrier deck or an airfield ashore. The Admiralty was sufficiently interested in this potential solution to devote money, manpower and resources to evaluate to it during a period of severe post-war austerity.
A flexible deck, more commonly referred to as a rubber deck, was built ashore at Farnborough onto which aircraft were to fly a low, flat approach well above the aircraft’s stalling speed to pass just over the rubber deck with their arrester hook down. The pilot was to treat each approach as a potential miss until he felt the retardation as his hook took the single arrester wire rigged across the deck. Shore trials were flown by Lieutenant Commander Eric ‘Winkle’ Brown DSC AFC RN who flew a modified Vampire prototype, TG 286, and several specially modified naval Sea Vampire F 21s. These had conventional undercarriages but were specially built with strengthened fuselages capable of withstanding the impact of wheels-up landings. The rubber deck was raised about 2 feet above the surrounding surface and the ideal approach height was difficult for pilots to judge. Both TG 286 and the rubber deck were damaged on one occasion when it dropped too low but the landings were generally considered successful enough to move on to trials at sea.
In 1948 HMS Warrior was fitted with a rubber deck made out of hosepipes laid across a steel frame over the conventional flight deck between the two lifts. They were filled with compressed air and covered by a rubber membrane on which the aircraft landed and the surface was lubricated for landings by hosing fresh water onto it. A single Mark 4 arrester wire was fitted over the rubber deck with the actuating pistons situated fore and aft alongside it. It had a maximum pull-out of only 160 feet which meant that a high minimum wind over the deck was required for every recovery. Warrior’s first rubber deck trials took place in November 1948 and the first landing was carried out by Lieutenant Commander Brown in TG 286, landing at an indicated air speed of 96 knots into a 35 knot wind over the deck which gave the arrester hook an entry speed into the wire of 61 knots. Once landed, the aircraft was lifted by crane so that its undercarriage could be lowered and it could then be manoeuvred onto the conventional area of flight deck forward of the rubber deck as normal. All subsequent landings were flown by Sea Vampire F 21s which were heavier and capable of being launched by the ship’s single BH 3 hydraulic catapult. A deck landing control officer or ‘batsman’ was positioned on the flight deck aft to monitor approaches and wave aircraft off if they appeared to go low. He did not give a ‘cut’ signal to the pilot to close his throttle since the aircraft was intended to keep power on and climb away if he missed the arrester wire. In two instances arrester hooks failed to catch the wire, the aircraft made contact with the deck and slid along it but the application of full power allowed them to climb away safely.
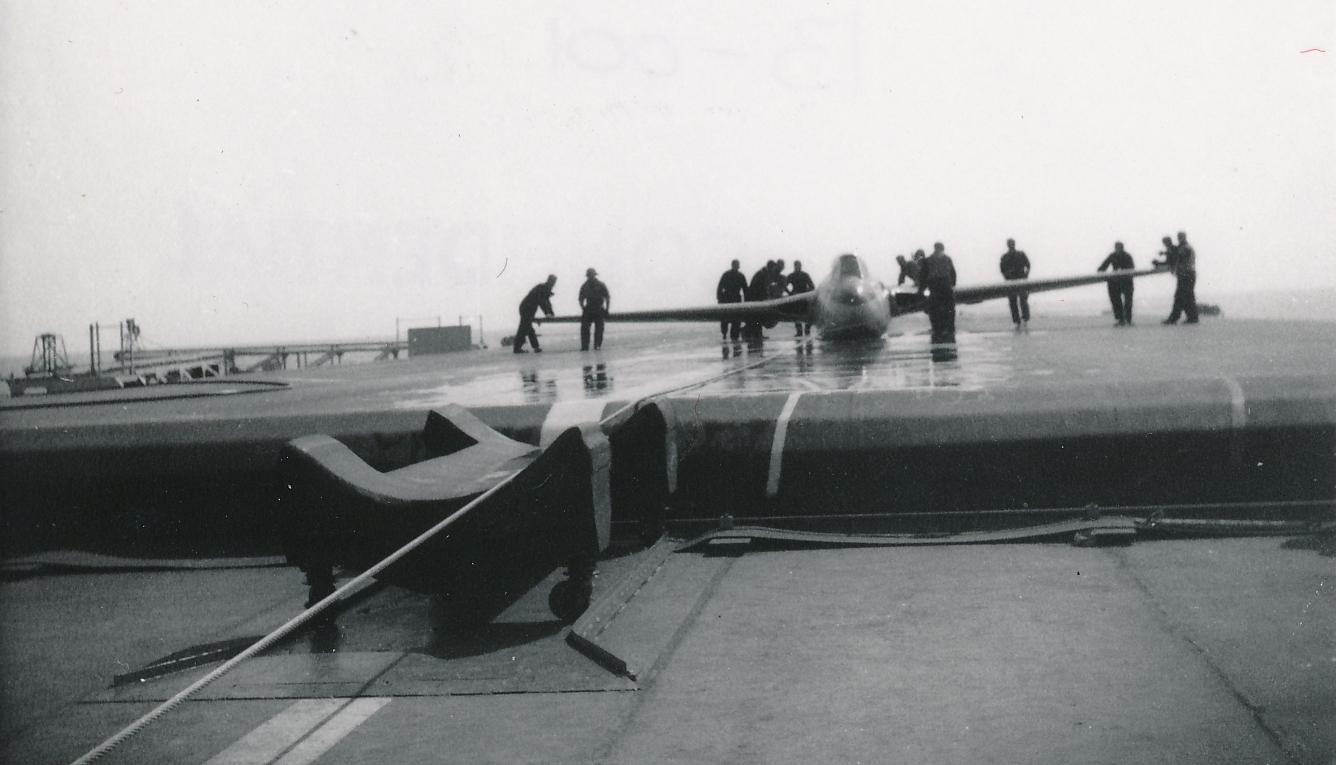
Further trials were carried out in March 1949; this time with two USN Mark 4 arresting gears mounted in tandem with the wire carried around the moving crossheads of both allowing a pull-out of 290 feet and an entry speed up to 120 knots. Five pilots with varying degrees of experience flew the aircraft this time in addition to Lieutenant Commander Brown and the USN sent observers to witness these trials. A number of safe landings demonstrated the practicality of landing undercarriage-less aircraft on a flexible deck but they also demonstrated the fundamental flaw in the concept. Normal landings by wheeled aircraft onto straight-deck carriers averaged about two per minute at the time. At closing speeds, relative to the deck, of about 60 knots this meant that as the first aircraft took a wire, the second should be turning finals 1,000 yards astern. Taking this distance as an acceptable minimum, Boddington argued that aircraft with a closing speed of 110 knots should be able to recover, theoretically, at the rate of one every 16 seconds, roughly four per minute. Assuming that the wave-off signal for a deck that was not yet clear was left until the following aircraft was in to 200 yards, this allowed 12 seconds to clear the rubber deck after each landing. The reality was that it took 5 minutes to clear each aircraft off Warrior‘s rubber deck, lifting them by crane while their undercarriages were lowered. Given the number of aircraft embarked, even in the smaller carriers, a landing interval of 5 minutes was never going to be acceptable and NAD thought of a number of ingenious ideas to overcome the problem, the best of which was the idea of canting the landing deck to port of the ship’s centreline so that so that aircraft could be pulled off it quickly into the parking area between the landing area and the island, designated Fly 2. The rubber deck concept was finally abandoned as impractical in 1954 but by then it had led to the brilliantly simple idea of the angled deck.
The Angled Deck
Jet aircraft with their higher landing speeds needed greater arrester wire pull-out space on the flight deck. Parking space ahead of the barrier, designated Fly 1, in straight deck carriers was, therefore, correspondingly reduced and the new aircraft in prospect could virtually eliminate the space available in Fly 1. If the RN was not to be forced to return to the clear deck techniques of the 1920s, a solution had to be found. Lateral separation with landing and parking areas alongside each other was suggested but was not possible on existing ships because they were not wide enough but a serving naval officer came up with a simple but elegant solution. Captain D R F Campbell DSC RN was the Deputy Chief Naval Representative at the Ministry of Supply, MoS, which was responsible for all British military aircraft procurement. In 1951 he was inspired by some of the concept designs put forward during the rubber deck trials in which the landing area had been offset from the centreline to allow aircraft to be pulled clear once they had landed.
Campbell worked with Lewis Boddington to put forward the very practical idea of radial separation. By rotating the axis of the landing area a few degrees off the ship’s centreline from a point at the after extremity of the flight deck, several positive and attractive benefits were achieved. Even a slight angle brought the forward edge of the landing area to the edge of the flight deck at a point well aft of the bows, lengthening the space available to bring aircraft to rest after they caught a wire. The area to starboard of the landing area formed a larger and safer Fly 1 extending into a new Fly 2 to port of the island which could also be used for parking aircraft after a land-on. The sum of the length of the two areas was actually greater than the length of the original flight deck. Even better, the angled deck gave pilots a clear deck with no barrier in front of them since aircraft parked in Fly 1 were parked to starboard of the wing tip safety line, clear of the line of flight. In straight-deck carriers a collapsible barrier had been used to protect aircraft parked in Fly 1 against an aircraft which had missed all the arrester wires crashing into them. With the angled deck, if an aircraft’s arrester hook missed all the wires, the pilot simply opened the throttle and climbed away for a further circuit.
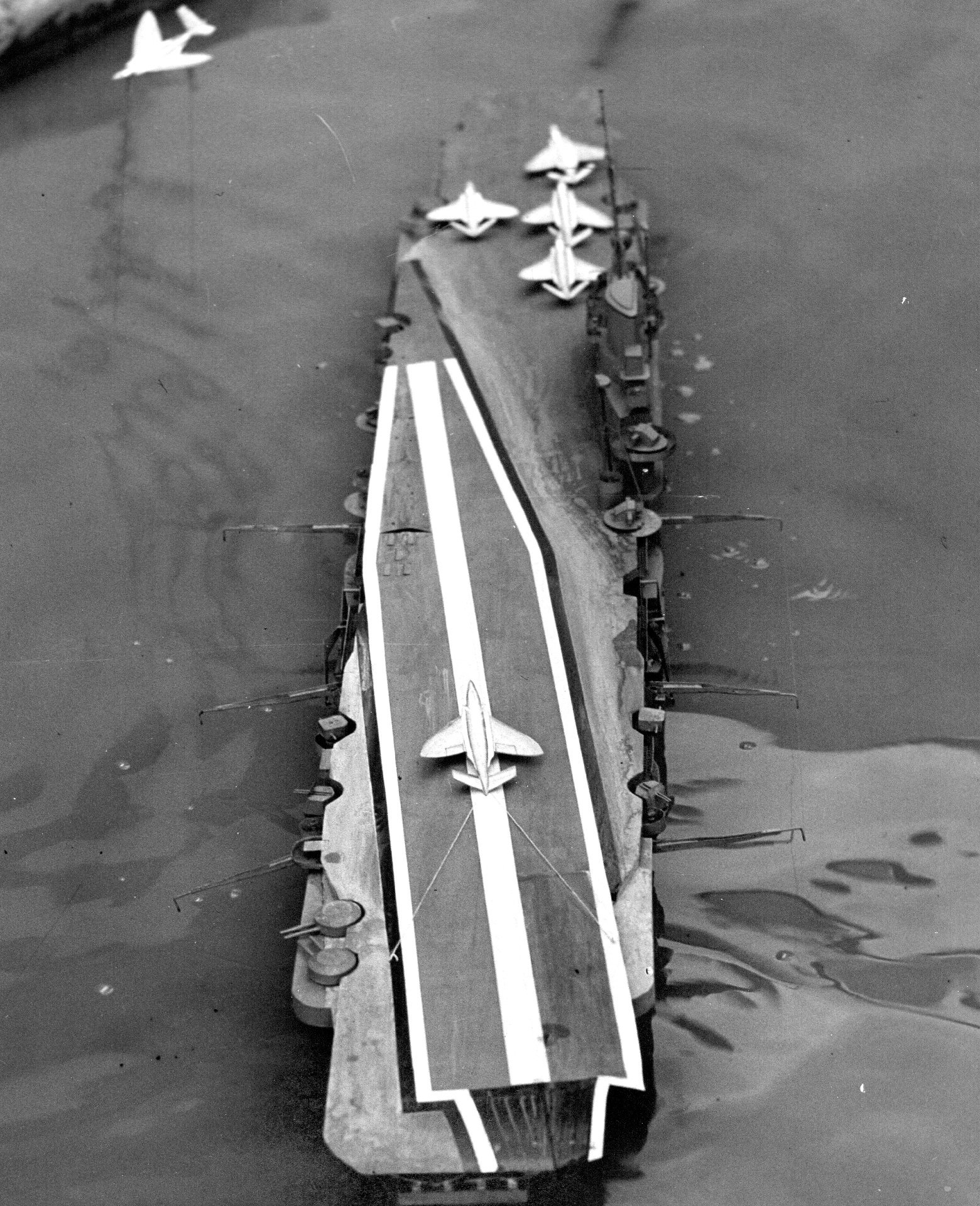
The concept was demonstrated by photographing a model carrier with an angled deck floating in a tank and by flying trials on HMS Triumph. An angled deck was painted into place with its centreline extending from the starboard side of the flight deck aft to a point on the port deck edge abreast the island and angled 8 degrees to port of the ship’s centreline. In February 1952 several different operational RN aircraft types and others that were under development took part in flying trials which involved approaches to Triumph‘s angled deck. The trials were extremely successful and no difficulties were experienced flying circuits to the angled deck, the new constant-power approach down a steeper glide slope proved easy to carry out and pilot confidence was greatly improved by the lack of a barrier ahead of the landing area. The USN was kept fully informed at every stage of the new development, quickly appreciated its value and adopted it immediately. Trials similar to those in Triumph were carried out on to a deck painted onto an Essex class carrier in the spring of 1952 and in the summer, another Essex class ship, the USS Antietam, CV-36, was fitted with a 10 degree angled deck and a series of trials with a variety of aircraft types followed. These included a visit to Portsmouth in the autumn and RN trials which included a large number of arrested landings by operational RN aircraft. Known initially as the ‘skew deck’ in the RN and the ‘canted deck’ in the USN, the simpler term angled deck was soon adopted by both navies and the concept was adopted immediately. The only delay was caused by the significant amount of dockyard work needed to build the port-side sponson that supported the forward end of the new landing area and to re-align the arrester wires. Since its invention all carriers built or modified to operate fixed-wing aircraft in every navy have been fitted with angled decks.
The Steam Catapult
The steam catapult was also the work of a man with wartime naval experience. Commander C C Mitchell RNVR had proposed the development of a slotted cylinder catapult to the Admiralty in the late 1930s but, with the minimal requirement to catapult the light naval aircraft. mostly biplanes at that time, the existing hydraulic catapults had been deemed adequate and the idea, although recognised as sound, was not progressed. However, with the greatly increased weight of naval aircraft after 1945 and the prospect of even heavier jet aircraft in the near future that would have to be launched by catapults, hydraulic catapults were recognised as being at the end of their development potential. Mitchell resumed work on his concept and was able to hasten the construction of a test item when he found that the Germans had used a similar catapult to launch V-1 ‘flying-bombs’. He acquired components through the British Intelligence Operational Survey Team and the result was a prototype catapult in which rams were driven along parallel cylinders by steam pressure. A cradle linked the rams so that they ran along their cylinders together and provided the structure on which the towing shuttle was fixed. This ran along a slot at flight deck level, pulling the aircraft forward by means of a wire strop which was looped at either end onto hooks on the underside of aircraft. Rubber seals ran along the tops of the cylinders which were forced open by devices on the leading edges of the cradle and resealed behind it to allow its passage without significant loss of steam pressure. High pressure steam was provided from the ship’s boilers and stored in large accumulators at up to 4,000 psi.
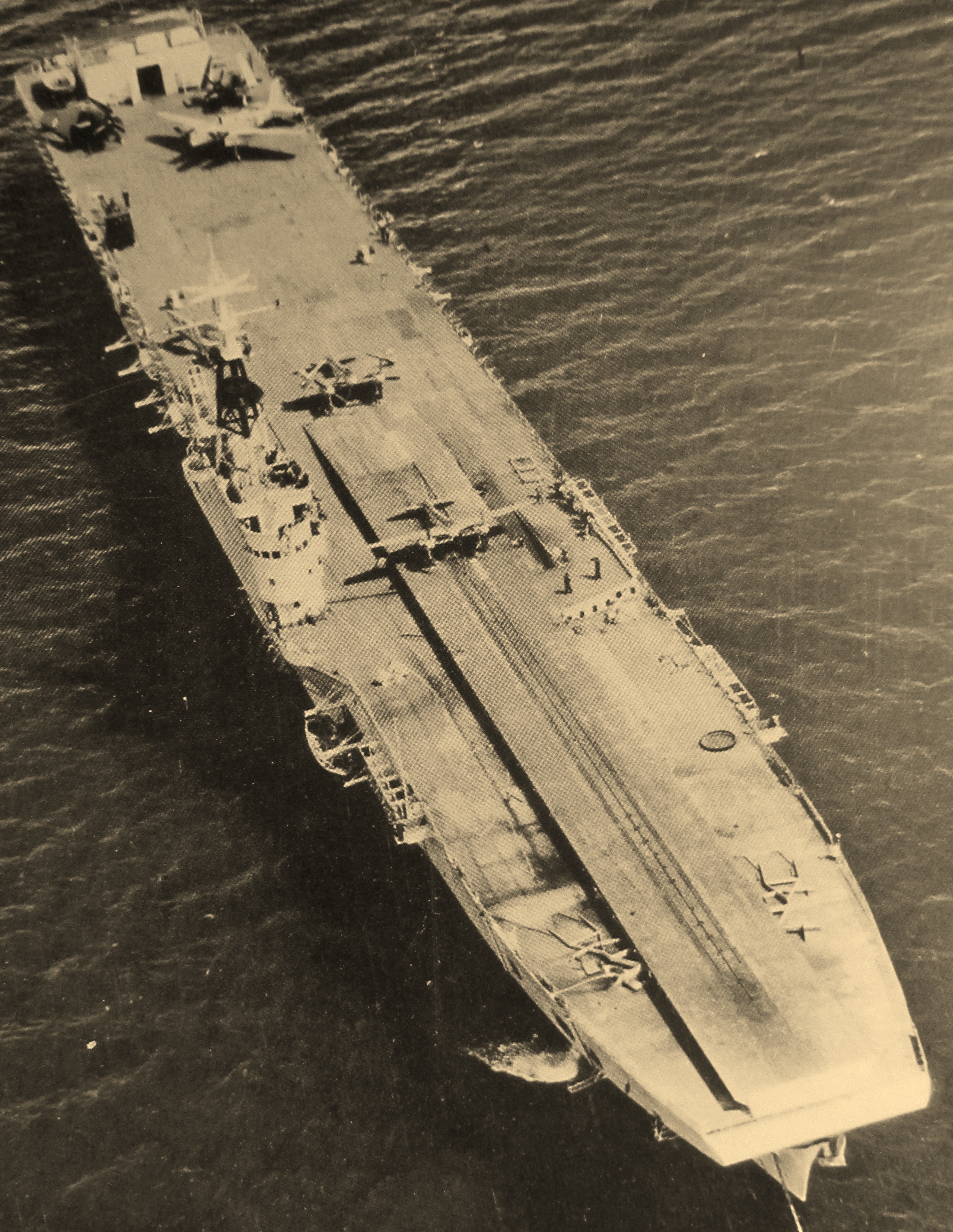
The hydraulic catapult had used a short piston which activated considerable lengths of wire-rope reeved between pulleys which translated the piston stroke into movement of the shuttle. Maximum acceleration was reached after less than a third of the shuttle’s travel and the wire pulleys were a constant source of unserviceability. The new slotted cylinder, or steam catapult, on the other hand not only had a greater energy potential but accelerated more smoothly to reach a maximum at two thirds of the shuttle’s travel. The Admiralty immediately saw the potential of the design and awarded a development contract to the Scottish engineering firm of Brown Brothers and Co which Mitchell joined when he was demobilised from the RNVR. After extensive trials with a development catapult ashore, the prototype steam catapult, BXS1, was built into a new structure on the deck of the aircraft maintenance carrier HMS Perseus in Rosyth Dockyard during 1951. Sea trials followed which at first used wheeled trollies known as dead loads instead of aircraft. These could be filled with varying amounts of water to achieve different weights which were carefully measured. Next came surplus aircraft with their outer wing panels removed. These were run up to full power and then launched without a pilot at increasing fuel weights. Finally, manned operational aircraft were launched at their maximum take-off weight.
The whole series of trials were carried out in conditions of strict secrecy and proved completely successful. A total of 1,560 catapult launches were made from Perseus, of which 1,000 were dead loads and the remainder unmanned surplus aircraft, mainly Seafires and Sea Hornets and the balance with manned operational aircraft including Sea Vampires. As with the angled deck, the USN was kept fully informed and had observers on Perseus throughout the sea trials. The RN made the ship available for USN sea trials and she arrived in the USA in December 1951. A further 140 launches were carried out using USN dead loads and operational aircraft; the data was found to correlate well with RN reports and the USN acquired the manufacturing rights for its own steam catapult production as part of the Mutual Defence Assistance Plan. Work began in the USA in April 1952; the first catapult was installed at NAS Patuxent River in December 1953 and the first launch from an operational carrier took place on 1 June 1954 from the USS Hancock. Despite the Admiralty’s enthusiasm, British industry was not capable of such rapid development, however, and the first British steam catapults went to sea in HMS Ark Royal in February 1955.
The British Carrier Strike Fleet is available now from Pen and Sword Books.